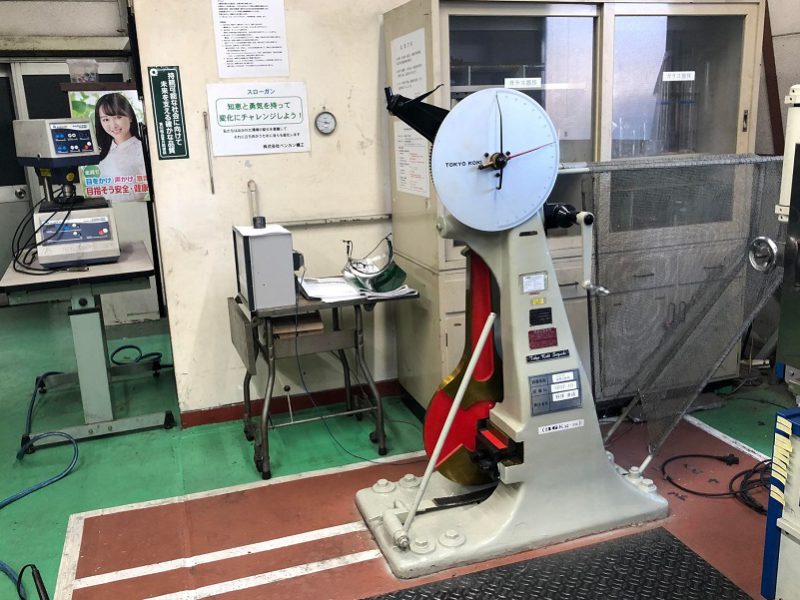
管継手を製造する際に、材料や製品の評価を行うために様々な試験を実施しておりますが、管継手に付随する各種試験のうち、機械試験は、製品の性能の一つである機械的性質を調べるためのものです。
機械的性質とは、金属が持っている力学的な性質の総称で、代表的なものは下記となります。
▼各機械的性質試験の相関関係▼
今回は、粘り強さ(靭性)を確認する方法である「衝撃試験」についてご紹介いたします。
衝撃試験とは、試験片に急激な荷重を加えた時の、材料の破壊抵抗性を調査し、ねばり強さ(靱性)、もろさ(脆性)を判定するための試験です。
衝撃試験を理解するために、まず、鉄鋼材の持っている性質をご説明します。
鉄鋼材は、常温では変形しやすく、十分な延性がありますが、低温になると脆くなる性質を持っています。低温になって脆くなった状態は、細いガラスの棒を折ることをイメージすると、変形せずポキっと脆く折れていく様を想像しやすいでしょう。このように、ほとんど変形せずに破壊する現象を脆性破壊と呼びます。(反対に、伸びながら破壊する場合は、延性破壊といいます)。
この脆性破壊は、微小な亀裂が生じた後に音速並の速度で亀裂が伝播し、破壊に至るもので、人の目ではその流れを捉えることはほぼ不可能であるため、一瞬でポキっと破壊されたように感じます。
この亀裂が瞬時に伝播することから壊滅的な被害となった例としては、有名なリバティー船の沈没がありますので背景からご紹介します。
第二次世界大戦に向かうアメリカは、戦争遂行のための莫大な戦時物資輸送を担う船を、多量に効率よく生産する必要に駆られ、アメリカの国家プロジェクトとして、戦時標準船を作り出す、緊急造船計画を打ち出しました。緊急に多量の船を造船するために、単一の非常に単純な設計で、海洋用途を製造したことが無い企業・労働者により、ブロックを作り出し、それらのブロックを造船会社が組み立てるブロック建造方式にて設計されました。
従来のリベット打ちは、工期と熟達を要するために作業者が不足してしまうため、その代わりに、工作時間が速く、労働者の習熟が早い溶接が、すべての金属接合箇所に採用されました。
なお、ブロック建造方式とは、現在の造船業では、一般的となっている生産方式で、船体をいくつかのブロックに分けて、それぞれ完成させた後に、全てのブロックを溶接で結合し、一隻の船を完成させるという建造方式なので、多量の船を効率的に造船するという目的に適していたと言えるでしょう。
16の造船所で組み立てられた全溶接構造の同型船は、1939~1945年の6年間で2,708隻が建造され、これらすべてはリバティー船と呼ばれています。
これらの急造された兵員・兵器・燃料の輸送船は、戦時のロジスティックに大いに貢献し、ナチスに占領されていたヨーロッパ奪回のための大物量作戦であるノルマンディ上陸作戦(戦争終結までに、人員は250万人、車両は50万台、物資は400万トンを上陸させた)を代表する数々の作戦で活躍し、初号機の造船時に新聞によって名付けられたリバティー船(自由を勝ち得るための船という意味)という名称の通りに、連合国の勝利に貢献しました。
しかしながら、1946年4月1日までに、リバティー船の脆性破壊の損傷と事故が1,031件も報告され、そのうち200隻以上が沈むか、または使用不能という重大な損害を受けました。これらを受けて、事故調査委員会が事故原因を調査し、3年後に報告しています。
この事故調査報告は、構造上の応力集中の減少策、溶接割れなど工作不良による初期の欠陥削減策、溶接残留応力の軽減策、脆性破壊防止には、リムド鋼よりもキルド鋼が望ましいというような報告と、溶接構造が主原因となった破断は少ないと結論付けていました。
アメリカでは、工学における失敗をその後の教訓として生かすべく船体構造委員会が発足し、1946年に最初のレポートが発表され、現在までに500を超えるレポートが発表され、フラクチャー メカニズム(破壊力学)の発展に寄与しています。
低温での脆性破壊の代表的な例が、ジョンP.ゲインズ号です。完成後6か月たたないうちに、気温0℃でうねりが船首を洗うような海況のアラスカ沖で、貨物ハッチの角から発生した割れが、鋼板を伝播して船体を破壊し、船首は沈没、船尾はアラスカに漂着したという事故がありました。
また、鋼材の溶接性不良と溶接残有応力による事故は、スケネクタディ号が最も有名です。この船は荷下ろしが終わり、岸壁に係留中に、穏やかな海況であったのにも関わらず、突如大音響とともに船体が真二つに折損しました。戦時中にも関わらず、新聞で報道されましたので非常に有名になりましたが、このような瞬時の折損事故は、航海中のマンハッタン号など、合計7隻に発生しました。
溶接部に沿って破断しているために、当初は海上保安庁より溶接施工不備とされていましたが、溶接部及び熱影響部の靱性不足による脆性き裂の発生と進展による脆性破壊で、溶接性が悪い鋼材と溶接残留応力が主原因であり、これに加えて応力集中を生ずる構造設計不良と溶接施行不良が二次的原因であると考えられています。
アメリカの船体構造委員会は、各種実験の結果得られた情報から、脆性破壊防止には、使用する最低温度でのシャルピー吸収エネルギー値が 20J(15ft・lb)以上必要であると結論づけました。
当然、構造設計で、応力集中する角を無くしたり、溶接施工・溶接後熱処理により溶接応力を除いたり、各船級協会が設定したシャルピー吸収エネルギー値が 20J以上の「特殊品質」の鋼板を構造部材に使用した船であっても、船体の脆性破壊は収束に向かわず、1954年の11月末には、ワールド・コンコルド号が、アイルランド沖で船体が真二つに折損しました。
この事故を調査したロイド船級協会は、溶接船に使用される鋼板は、0°C で47 J以上のシャルピー吸収エネルギーが必要であるとの結論をつけ、その後の1959 年に 国際船級協会(IACS)により 軟鋼に関する規格が UR(Unified Requirements:統一規定)1 として統一されました。
そのような歴史があり、シャルピー衝撃試験が、低温靭性・脆性破壊を防止する観点から鋼材試験に採用され、造船のみならず低温サービスで使用される鋼材に一般的に要求される試験になりました。
このシャルピー衝撃試験は、今から100年以上前の1901年に、フランス人のシャルピー技師が発表した論文にて、公開された試験方法で、振り子のエネルギー保存の法則を利用し、(振り子の最初の位置エネルギーが、運動エネルギーに、運動エネルギーは速度の2乗に比例して位置エネルギーに変換される。つまり抵抗が無ければ、振り子は、反対側の同じ高さまで上がり、また元の位置に上がってを繰り返す)、振り子の上がり方で吸収エネルギーを求める方法を考案しました。
使用する試験片は、断面に切欠きを入れることで、この切欠きの箇所に応力集中を生み出し、それによって鋼材の微細な欠陥やハンマーのあたり具合の違いによるばらつきを避け、狙った箇所を破断させることで、比較的安定した試験結果を得ることを目的にしています。
なお、それでも、試験片毎にばらつきが生じますので、シャルピー衝撃試験は、3試験片で1セットという単位で、個別での最低吸収エネルギー、3個平均での最低吸収エネルギーが、規定されています。
現在では、主流は、2mmVノッチといい、V型のノッチ(Vでもノッチ底部にはRがあります)を試験片断面に刻みます。また2mmUノッチという試験片形状もあり、これは主にロシア向けで要求された試験片形状でした。
この切欠きの応力集中は、切欠き効果(ノッチ・エフェクト)といい、ノッチの形状、角度、底部のRが異なると、当然異なった応力集中となり、試験結果に変動を与えますので、試験片のノッチ形状は、試験前にプロジェクターで確認するのが一般的だと認識しています。
試験温度は、0℃以下の温度は、ドライアイス(沸点-78.5℃)とエチルアルコール(凝固点-114.5℃)を使用して、-70℃までの冷却に使用し、-162℃の液化天然ガス(LNG)用の配管のために、液体窒素(-196℃)を使用しています。
地球温暖化させないようにCO2排出量を削減する機運が日々高まっており、日本でも水素社会を官民一体となって構築しようとしていますが、気体を最も効率的に運ぶ方法は、液化することであり、天然ガスの場合は液化することで容積が約1/600になり、水素の場合は、約1/800となります。しかしながら水素の液化温度は-253℃で、この環境を確認するには、液体ヘリウムを使用した- 269℃での試験が要求されます。ベンカン機工の自社設備では-196℃までの試験は日々行っていますが、液体ヘリウムを使用した- 269℃のシャルピー衝撃試験は、協力会社にて実施してもらっております。
実際の鋼材の持つ低温靭性は、温度により変位していき、より低い温度では、脆くなり、温度が室温に近づくと延びる様になります。そのため、鋼材の特性を把握するためには、シャルピー衝撃試験を様々な温度で実施し、シャルピー遷移曲線のグラフを作成します。破面が脆性破壊と延性破壊の50:50の位置を、破面せん断温度と呼び、最低使用温度が、破面せん断温度よりも高ければ実際の脆性破壊の危険性は少ないと定性的に把握できます。鋼種に要求する試験温度は、このシャルピー遷移曲線をもとに設定できますので、現在では、一つの試験温度でシャルピー衝撃試験を行い、過去の痛ましい事故の調査結果から得られた要求衝撃吸収値を判定基準として採用し評価しています。
シャルピー衝撃試験では、吸収エネルギーのみならず、破面の様相(脆性破面・延性破面)、変形挙動(横膨出量)、亀裂の進展挙動(延性破面率)によって、脆性破壊しやすいかどうかを評価することができます。
なお、管継手には要求されることはありませんが、低温靭性を調査する試験としては、CTOD試験(破壊靭性試験)とDWTT試験(落重試験)があります。シャルピー衝撃試験は、瞬間的に加えられる衝撃に対する抵抗を測定する試験に対して、CTOD試験は、切欠きを持った試験片をじわじわ曲げて、切欠きの開口量を調べることで、延性的な破壊抵抗を調査するための試験になります。またDWTT試験は、脆性破壊の伝播しやすさを調査するために、タワーから重錘を落として、延性破面と脆性破面の破面率を計算し、破壊伝播を評価する試験です。どちらの試験も通常管継手に要求されるものではありませんので、弊社では検査設備を保有しておりません。
日本では一般的なJIS B 7722シャルピー振子式衝撃試験-試験機の検証に準拠して据付・検証し、検定を日本海事協会殿にて実施したシャルピー衝撃試験機(能力:500J)のみならず、NIST(アメリカ標準技術局)が定めるASTM E23に基づく信頼性評価に適合したシャルピー衝撃試験機(能力:360J)も据付、保有しておりますので、JIS規格のみならず、ASTM、ASME規格でシャルピー衝撃試験が要求された場合でも、自社内で対応可能です。
テクニカルシートのダウンロードはこちら↓
各種鋼材材料でのシャルピー衝撃試験リーフレット
技術本部
最新情報をお届けします